AIS Case Study - Confined Space Leak Survey using Drones
Objective
Confined space drone inspection survey as part of a scheduled asset integrity management programs.
​
The Project
This example shows us performing an integrity survey of a vertical shaft bearing assembly on a rotary heater inside a 510-Megawatt gas fired power station.
​
Key Results
-
Detect, validate, quantify, geo-tag, and report oil leaks from the bearing and casing assembly while flying inside the rotary heater.
-
Annotated photos of potential leak sources.
-
Marked-up drawings.
-
High-definition videos of the observed leak locations.
-
Quickly, safely and cost effectively locate leaks inside structures
-
Quantify shut-down work scope.
-
Save overall labour (cost) and reduce risk using experienced leak detection personnel and dedicated technology.
-
Expedite maintenance shut-downs through early issue detection in the inspection and test plan (ITP)
-
Capture visual context of asset integrity issues,
-
Measure deviation to prioritise and scope repair costs.
-
Manage occupational risk by eliminating the need for confined space entry of inspection personnel.
Key Challenges
Hazardous Environment
-
Confined Space.
Hazardous work areas
-
A Pitch black working environment.
-
No detailed as-built drawings of the asset.
-
GPS denied environment.
-
Tight working space with obstructions.
-
Working in proximity to protruding surfaces
-
Working at Height
-
Noisy environment
AIS Survey Solution
Confined Space Drones
-
On-board adjustable lighting.
-
On-board LiDAR scanner to generate a point cloud.
-
On-board gyro-stabilisation.
-
Flight referencing the LiDAR point cloud.
-
Experienced Drone pilots performing precise and accurate flight inside the workspace.
-
On-board thermography.
Risk Management
-
AIS is experienced operating drones in hazardous Oil & Gas Process plants and Petroleum Refining Plants.
-
Comprehensive JSEA Job Safety & Environmental Assessments.
-
Civil Aviation Safety Authority approved drone operations risk management system.
Value Added
Risk minimisation
-
Eliminate requirement for inspection personnel to enter the confined space.
Cost Savings
-
Significant cost & time saved by eliminating scaffold erection inside the workspace.
​
Reporting & Data Visualisation
-
Marked-up conventional 2-D images, video and 360 Degree panoramic SiteView scenes of leak locations.
-
Contextually rich scene information that facilitate risk assessment and repair action prioritisation.
-
360 Degree panoramic SiteView of the point of interest providing a visual reference for all personnel when developing remediation work scopes.
Related AIS Shutdown Services
-
Plant shut-down work-pack collaboration and digital twin reality capture services.
-
Confined space asset surveys using reality capture sensors on remote operated vehicles: AISS-ROV 360
-
Regulated Leak Detection And Risk Management (LDAR) monitoring programs.
-
Inert Gas- Instrument Air, Compressed Air.Ultrasonic Leak Detection.
-
Flare tip condition monitoring programs.​
-
Gas Turbine Leak Surveys
Contact us to discuss how we can help you with your asset integrity management programs
Client
Gas Fired Power Station
​
Work Site
510 MegaWatt Power Station
Victoria, Australia
​
Type of work
Shut-Down Asset Integrity Surveys
​
Scope of work
-
On-Site Risk Management, JSEA, Permitting
-
Leak Detection
-
Quantification
-
Leak Risk Assessment
-
Asset Condition Capture
-
Contextual Reporting
-
Repair Action Priority Assessment
-
Asset Integrity Verification
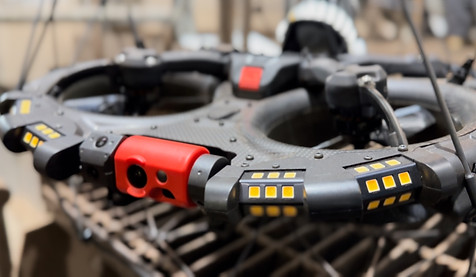

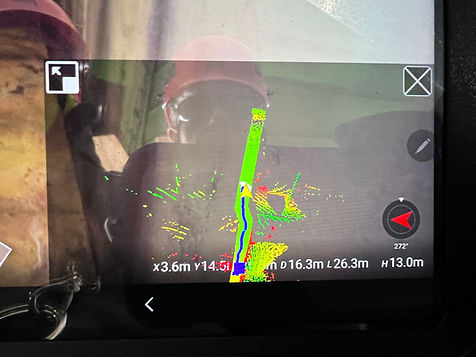

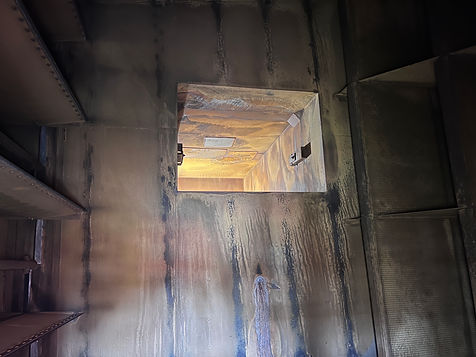