AIS Case Study
Ammonium Nitrate (Explosives) Production Facility
Leak Risk Management Survey
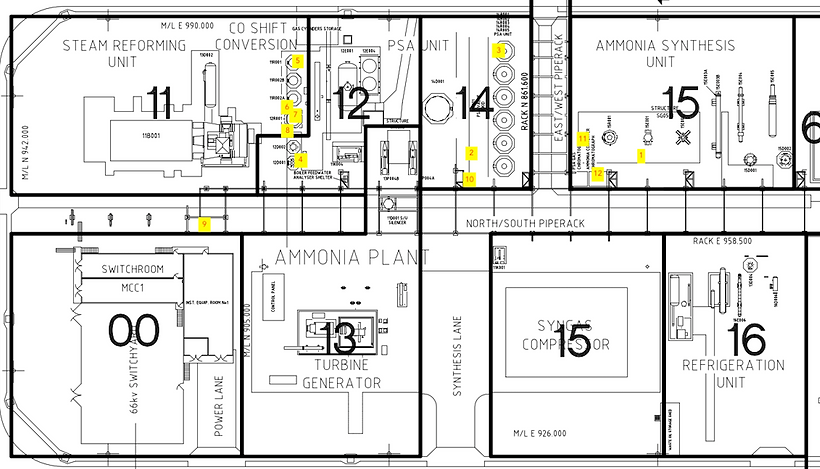
Survey Scope & Results - Overview
Objective
• Establish a “baseline integrity condition” of the syngas / shift conversion process.
• Reduce immediate leak risk.
• Scope leak remediation work pack activities for forthcoming plant tern-a-round (maintenance campaign)
​
Project Scope
• Locate, identify, quantify, report, and risk assess syngas leaks from components in the feed gas, recycle gas, and syngas loop processes.
• Prioritise and validate the repair of high-risk leaks prior to the plant turn-a-round
• Prioritise medium or low risk leaks that cannot be repaired immediately scope for inclusion in plant turn-a-round work packs
​
Key Results
​• The survey reported multiple leaks to atmosphere from pressurised process components across 5 process units.
• Leaks to atmosphere and from Pipe Flanges, Pressure Vessels, Process Valves and Instrumentation.
• Leaks across normally closed valve seats including pressure safety relief valves, process check valves, and manual block valves.
• Recommended remedial options for work pack scope input before the scope freeze date.
• Reduced immediate process integrity risk by fixing high-risk leaks prior to the plant turn-a-round.
• Risk context-based prioritisation of Turn-a-round work scope packs.
Key Challenges
Hazardous atmosphere
• Potential for explosive gas leaks.
• Potential for Hydrogen rich (Syngas) leaks.
Hazardous work areas
• Surveying in proximity to Hot or Cold Surfaces
• Surveying at Height
• Surveying live process equipment
• High process pressures
• Potential leak points located in restricted or confined spaces
• Noisy environment
Leak Detection and Quantification challenges
• Hydrogen rich (Syngas) and Raw feed gas (Methane) gas is invisible and odourless.
• High noise environment can mask audible leaks
• Accurate gas loss quantification is challenging because Hydrogen and methane leaks are highly buoyant and disperse quickly
AIS Survey Solution
Acoustic Leak Detection
• AIS deployed intrinsically safe ultrasonic (acoustic) scanning technology to locate and validate gas leaks which are inaudible or masked by process plant & equipment noise.
Sensitive Detection Technology
• AIS deployed portable gas analysers to validate and quantify Hydrogen and Methane process gas leaks at levels as low as 2 parts per million (ppm)
Online survey – No interruption to production.
• AIS surveyed for leaks with the process online and without interrupting production.
Appraisal Criteria & Value Added
Safety & Risk Management
-
Engaged with HSE supervision and principal contact personnel to deliver a safe and cost-effective leak risk management survey.
-
Survey performed safely and condition reports delivered with zero HSE incidents.
-
Enable context-based risk assessment, prioritisation, and repair of high priority leaks prior to the turn-a-round.
Reporting with visual risk context
-
Leak location and asset identification through interactive 360 degree panoramic reports.
-
Ranking reported leaks in accordance with agreed repair action prioritisation assessment (RAPA) criteria.
-
Objective serviceability assessments of the leaking asset,
-
Indication of the possible root cause of the leak
-
Suggested remedial action to fix the leak.
-
Leak risk assessment and repair action prioritisation in accordance with client process integrity management policies.
-
Reporting complete with marked-up 2-D images, 2-D video and 360 Degree panoramic Siteview interface of each leak location.
Related AISS services
-
​Plant digital twin reality capture and SiteView services to enable shut-down work-pack planning & scope development.
-
Confined space asset surveys using reality capture sensors on remote operated platforms – Drones and ROV’s
-
Thermographic anomaly surveys of critical process equipment – Switchboards, Motor control systems.
-
Inert Gas- Instrument Air, Compressed Air. Ultrasonic Leak Detection.
-
Flare tip condition monitoring program with AIS Drone services.
-
Storage tank coating condition monitoring programs.
Contact us to discuss how we can help you with your asset integrity management requirements.
Client
• Explosive grade ammonium nitrate producer
Work Site
• 210,000 tonnes per annum Ammonium Nitrate Production Facility, Australia
Type of work
• Pre-turn-a-round leak risk management survey to fix high risk leaks and scope medium or low risk leaks for turn-a-round work pack inclusion.
Scope of work
• Site and Process specific JSEA, HSE management and permitting
• Syngas (Hydrogen) & Methane Gas Leak Detection
• Gas Leak Quantification
• Gas Leak Risk Assessment
• Asset Condition Capture
• Contextual Reporting
• Repair Action Priority Assessment (RAPA)
• Remedial recommendations
• Risk context-based work scope prioritisation

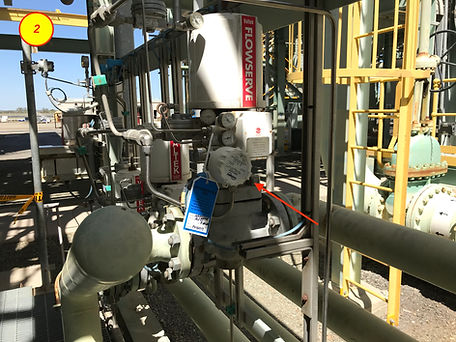
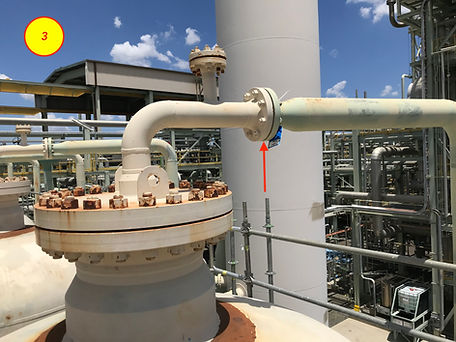

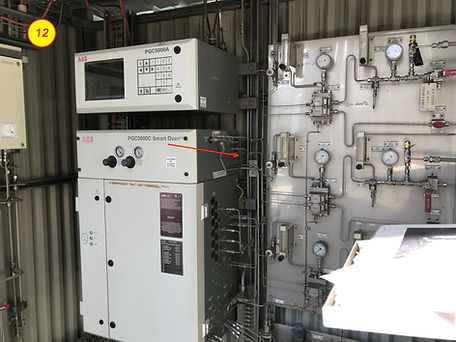